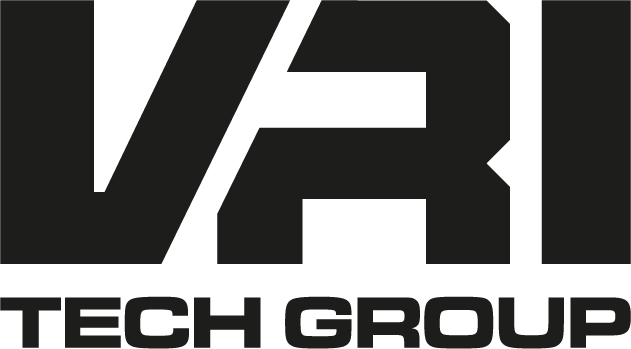
Een groep van hoogwaardige bedrijven in aandrijf-, hijs- en heftechniek.
Movit offers flexibility to set up and adapt your production line to your own preference. This allows you to respond to anychanges and it supports continuous improvement with active participation from your co-workers using the line. It will also allow you to approach automation step by step.
Movit is an intelligent modular transfer system for application in assembly and production processes. It will support almost any production or assembly process with step by step handling of the products between these processes. It is easy to expand or adapt to changing requirements into another configuration. What stands out is Movit's modular design and intelligence that will allow fast reconfiguration, addition of work cells such as cobots or process elements. Each element has its own control and is equipped with I/O link to help those changes. This encourages continuous improvement rooted in the experience of the users themselves.
Movit uses proven system components to move a carrier from process step to process step and keep track of production data. By employing RFID tracking quality validation becomes easy to track and each individual product can follow its own track if required. The PLC control is configured to support change in the configuration; either by remote service by Wadcon Automation or yourself using the optional digital twin. This allows you, for example, to program in a cobot to take over and automate manual screwing or to grind and polish your product on the line. You can approach your automation step by step.
Wadcon Automation designs production automation equipment. We created Movit to support our mission to help our customers to optimise their assembly, inspection and testing work.
The modular track elements are combined to build a production line that is suitable for your requirements. There are quite a few possibilities so that we prefer to make the system choices together with your engineers.
The carrier belt units are assembled to form the base of the production line. Each unit is equipped with its own motor and drive unit. The belts carry the product carrier to where it needs to go and are designed to slide under the carrier with low friction when the carrier is stopped. Each unit has its own control unit, frequency drive and I/O link and can be individually controlled.
The carrier lies on the drive belts and is transported from process step to step. Guide pins ensure that it follows the track and controllers can use the guide pins to move it sideways or turn corners, similar to a rail switch. Standard carriers are up to 400 x 400 mm with maximum 50kg load. Custom carriers are available.
The stopper positions the carrier for work or buffering. The basic stopper is pneumatic and ensures positioning up +/- 5mm while the drive belts slide under the carrier. Stoppers with soft-stop are available and if required the belt can be slowed using the frequency drive.
Sometimes accurate and stable positioning is required for work on the product. For this we offer a positioning system that lifts the carrier off the belt and holds it in place accurately. Typically we would combine this with a handshake protocol for a cobot that will do the process work.
The carriers are guided by a set of cams, using the guide pins to a 90 degree turn. This is used to guide the carrier onto a new belt drive at a right angle.
The product carrier is turned around to a parallel return track by using a combination of guiding cams and tracking pins with a short drive belt.
The switch is controlled by electrical control to allow the carrier to make the switch to a parallel track. This can be used to create a parallel production track with extra work spaces. The switch is controlled by the production line PLC based on RFID reading of the tag.
With this unit each carrier will be led via the switch to a parallel track.
The carrier is stopped at the assembly location and taken off of the production line by a side shift that uses the cams and guiding pins of the carrier along with a pneumatic cylinder. The carrier is pushed off the line onto an assembly location that uses vacuum to firmly position the carrier. Often the carrier will be integrated with a production mould. This allows assembly work to be carried out that requires a stable base. On a signal from the assembly worker, a stopper will hold incoming carriers and allow the carrier to shifted back on the track.
such as an emergency stop or a light screen are integrated and defined into the PLC control of the production line. For example a robot will be protected by a cage and safety switches on the door of the cage. The control unit has these features integrated and pre-programmed.
Wadcon Automation is known for designing custom automation solutions. Please feel free to challenge us with your handling automation puzzles to integrate into the Movit line.
The basic Movit production line is equipped with a programmed PLC that serves your line and all its components, including handshakes for the production equipment. The software is designed to serve your system remotely and facilitate any changes you wish to make to the system quickly and efficiently.
The I/O link technology integrated in this system makes sure that any changes or additions to the configuration do not result in rewiring the entire system. We simply connect the linking units and adapt the PLC program to suit.
Each track element has its own control unit with I/O link, frequency drive end motor controllers. This allows it to be able to work independently. With this feature we facilitate fast changes to the production line.
Movit allows the placing or removing of control elements such as a stopper or sensor in the same modular manner, connecting up via the I/O link system. The PLC software is updated and the production line ready to go again.
The use of the I/O system connecting all the sensors, RFID readers and control elements is an essential part of this product: we can make changes quickly and without the drama of rewiring the entire line. The I/O link connects up all the elements with a single signal cable so that all we need to do is adapt the PLC system control to suit. In this photo the green wire is the signal cable: one going in and one going out.
The PLC ensures that the production line is controlled overall and melds the component units into a single system. The PLC controls the flow of production carriers based on its programming and signal received from the sensors and RFID system. It reports the production data to a memory card (or a data base) for production validation data or QA purposes.
A 'Handshake' integration of Cobots or robots is part of the line: whenever any equipment is integrated a handshake protocol is required so that the equipment knows when to start and can communicate when it is finished, along with the accompanying production data.
Movit can be programmed for use by Wadcon Automation and any adaptions can be done by our remote service. If you require a change we can make the required programming changes quickly and efficiently from our base. This will mainly be defining new handshake protocols or adjusting the position of sensors and functions after changes to the layout.
Movit Intuitive (Digital Twin) Control goes a step beyond that: Using a digital twin you can (re)define the whole system on a tablet or PC using 'drag and drop' technology with a graphic menu control. When you are satisfied with your new configuration and that it matches the physical situation you simply let the program rewrite itself for the new configuration. The digital twin also helps trouble shooting on site. This is unique in the production line business. For more information please check: https://www.wadcon.eu/innovation/movit-transfer-system/movit-control.
Should you have any questions or enquiries on how Wadcon could improve your industrial processes, please don’t hesitate to contact us and we shall revert fast.